Montaje de equipos electrónicos
EMS (Electronic Manufacturer Subcontractor)
ALCOELECTRO se dedica al montaje y la fabricación de equipos electrónicos para empresas de múltiples sectores industriales: telecomunicaciones, electrónica de consumo, informática, señalética, electrónica industrial, IOT, electromedicina, ferroviario, entre otros. La flexibilidad y escalabilidad de Alco, le permite fabricar desde prototipos hasta grandes series, brindando una solución global a las necesidades de producción de sus clientes.
El alcance del servicio es también personalizado, desde un servicio llave en mano del producto terminado, hasta un simple Rework de una serie de fabricación.
Alco pone a disposición de sus clientes su experiencia en industrialización de productos para intentar optimizar costes, calidad y TTM (Time To Market)
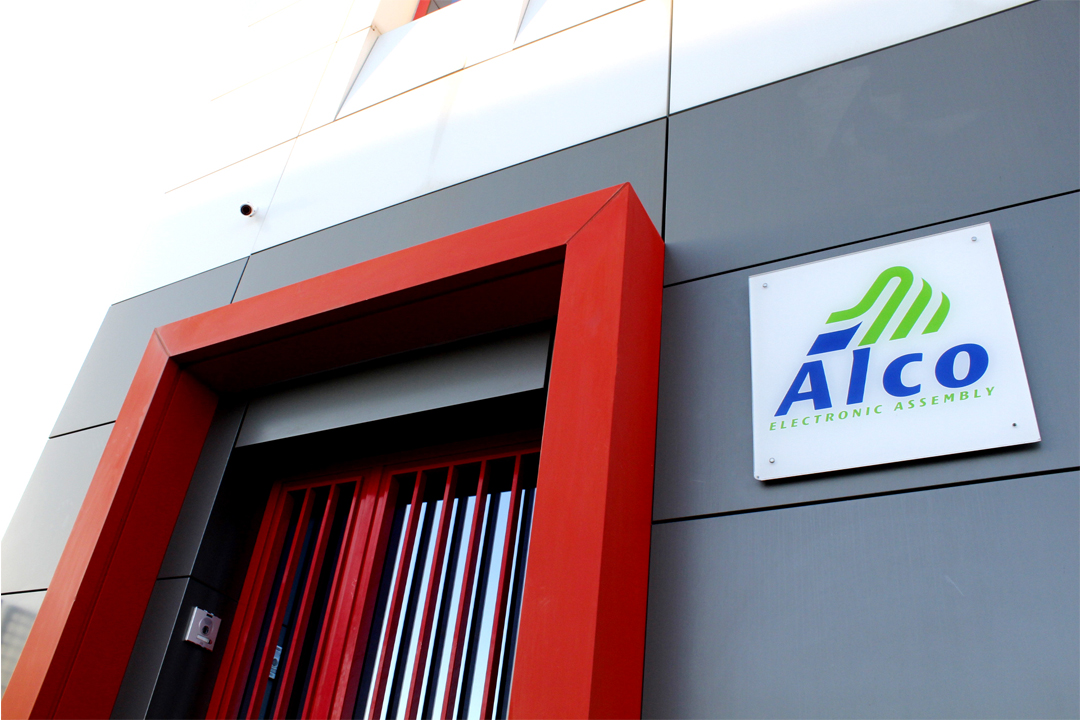
Desarrollo y fabricación de Módulos LED HD:
Diseño de circuitos / PCB Design
Fabricación de prototipos rápidos CNC PCB
Fabricación de series / small-medium and large batches
Test automatizados - Manuales seguros al 100%
Pegado y fijación de lentes
Instalación de disparadores / Heat Sinks Assembly
Servicios
Fabricación de productos electrónicos
Asesoría en la Industrialización de Tarjetas Electrónicas
Gestión de Compra y Logística de materiales
Montaje SMD y Convencional (TH), según normativa RoHS
Verificación Funcional, a pedido del cliente
Servicio de montaje de prototipos en 24/48 Horas
Trazabilidad de componentes
Contáctanos
ALCOELECTRO S.L.
Calle Puerto de Cotos Nº 12. Polígono Industrial Las Nieves, Mostoles 28935 (Madrid).
+34 91 778 03 74
+34 91 223 71 53
ventas@alcoelectro.com